Green woodsmith eases technology blues
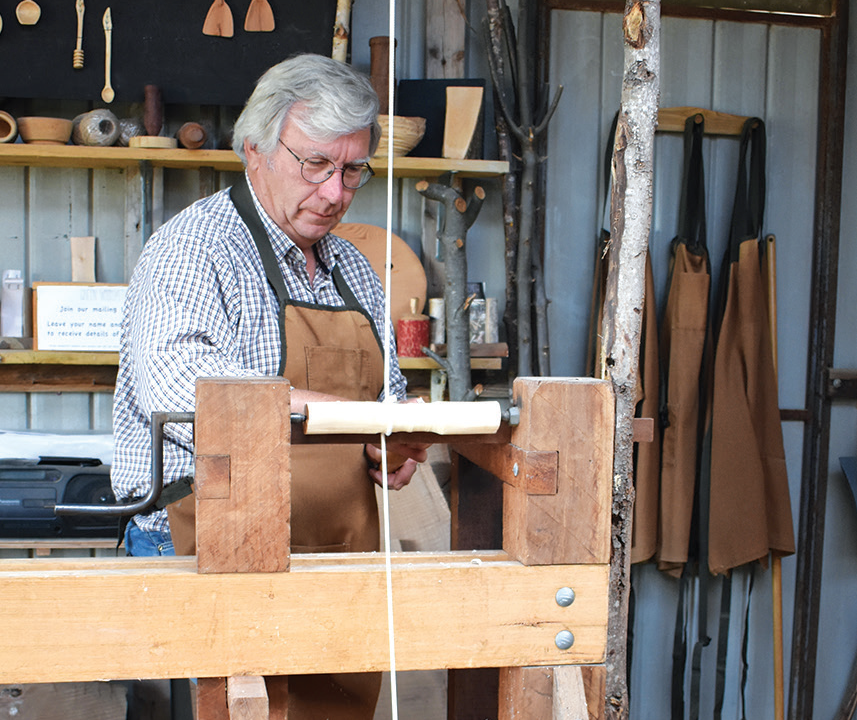
Pedal power: Paul Ryle operating one of the three pole lathes he made for use in his workshop Photo: CAROL SAFFER
PAUL Ryle is a self-confessed total and utter wood geek.
“Whereas most kids spent their paper boy money or spending money on sweets or comics I went and bought wood working tools.”
Mr Ryle has been a wood worker since he was eight years old.
During his childhood holidays in England he remembers meeting up with old trades craftsmen the likes of charcoal burners and bodgers.
A bodger Mr Ryle explains, is someone who bought a stand of wood – a parcel of living treesset up camp, cut the wood, split it into segments and using a pole lathe hand built on site, turned the wood into chair legs by the score and sold for a few pence.
This was where his interest in the social history and his capability in woodland crafts all began.
A medical researcher in a past life in Cambridge, Mr Ryle and his family emigrated to Australia in 2006 settling in Buninyong where together with his wife Jenny and their kids took two years to build their straw bale house.
After that he built a workshop establishing himself up as a green woodsmith.
“Green woodsmith means I am working with freshly cut unseasoned timber and I’ve been doing it for 30 odd years.”
After visiting the inaugural Lost Trades Fair in Kyneton, he realised people were fascinated in something he has always done.
“I couldn’t believe people’s interest in heritage trades.”
He didn’t want to make things to sell – it was an interest in teaching people how to use these tools and how to make them, which lead him to running one-day workshops for three students at a time every second weekend.
“It’s a relaxing day in the country in a rustic old workshop where I just like passing on this craft to people,” Mr Ryle said.
His workshop is a cornucopia of all things wood, steel and leather.
There are tools that are have been designed for simplicity which Mr Ryle uses constantly.
Amongst his collection is a froe knife for splitting timber along the grain, an adze – something like an axe used for carving or smoothing wood and his favourite stock knife, used like a guillotine for making wooden tent pegs.
During both world wars there were millions of tents used to house soldiers which created a need for tens of million pegs, all made by hand with a stock knife.
He has three pole lathes, all self made using his own tools, which operate by a foot treadle that spins and shaves the piece of greenwood into the desired shape.
A most brilliant, ingenious simplistic yet effective tool.
His pleasure and enthusiasm for making and using these ancient and traditional methods is infectious and awe inspiring.
He also collects old tools whenever he sees them.
He loves them because they are so well made.
Mr Ryle makes garden dippers, replacement tool handles and spoons amongst many other things.
A crook knife is used for carving out the bowl of the spoon, however Mr Ryle said there is a world-wide shortage of tools to carve spoons at the moment.
“The trend for spoon carving has gone viral,” he said.
He can carve a spoon in two to three hours, his students take the whole day.
They learn how to handle the tools as there are lots of different grips – power grips, thumb push grips a bit like sharpening a pencil, thumb lever grips, moving onto the carving in the afternoon.
“Provided you learn these grips you will never cut yourself, I have a first aid kit here and have never opened it.”
Mr Ryle is a very practical type of person, carving things that are simple and practical.
He sharpens all his own tools honed to a fine very sharp edge on his wet stone grinder.
To protect the blade, he makes all the leather hoods for his tools getting the leather from Greenhalghs Leather tanners in Ballarat.
He makes it all sound simple – “It’s not difficult, cut some leather and put some rivets in” Mr Ryle believes these old crafts are coming back because there is so much technology in everything people do, they just want to have a break and make something for themselves.
“It is doing something that takes us away from the technology that has invaded our lives – this is so technology free.”
Shavings are created when using a pole lathe to turn the wood, it’s safe and its quiet.
“An electric lathe would create dust so you need a protective mask and protective glasses, all totally unnecessary when using the pole lathe.”
He finds his inspiration when he picks up a piece of wood – beech is his favourite.
“Even if it is something simple, I will start following the direction of the grain.”
He made his own spoons that the family use in the house and is often commissioned to make handmade corporate gifts.
“I like to potter about, so I’m actually thinking about making some tools, starting up a little forge next door,” he chuckles with gleeful wicked enthusiasm.