Sweeney shapes the bells
THE iconic trophies have been assembled, and history is ready to be made at this year’s Rip Curl Pro Bells Beach.
Jan Juc local Jeff Sweeney has put the finishing touches on the silverware ahead of what is sure to be a showstopping event.
Hand-crafting the bells has been in the Sweeney family for more than 40 years.
Jeff’s father Joe started making the iconic trophy in the late 1970s.
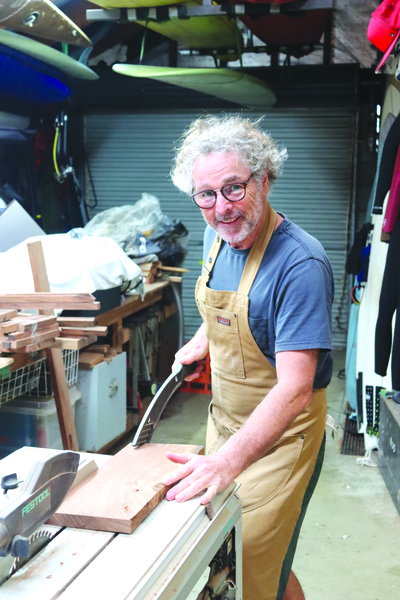
Photo: NATHAN RIVALLAND
A carpenter by trade, a teacher and an Olympic wrestler, Sweeney worked with Rod Brooks and Stan Couper to craft some of the first bells.
Sweeney was also responsible for helping to bulldoze the first access road to Bells Beach ten years earlier.
With his blessing, Jeff, his son has taken on the mantle over the past ten years, using his own boat-building skills to add his own personal touch to the fabled history piece.
He feels incredibly privileged to be carrying on the fabled tradition for his old man and all those before him.
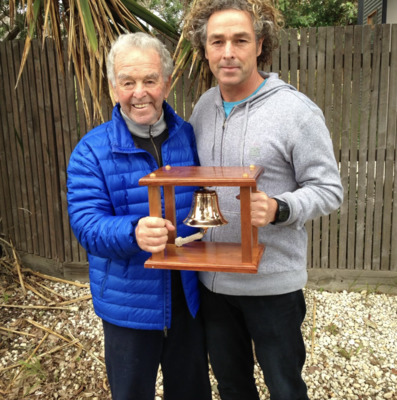
“It’s a nice tradition. I enjoy that dad did it and had so much passion for it.
“You talk to the crew on the world tour, and it’s one of the most sought-after trophies. That’s why I put a lot of passion into driving the quality.
“Both dad , Rod Brooks and I have won a surfing title of some kind at Bells, so it [making the trophy] comes from an authentic place. We’ve all spent plenty of time out there.”
Sweeney has crafted this year’s trophies using blackwood from the Otways.
He said the product is getting harder to source following the state government banning native logging.
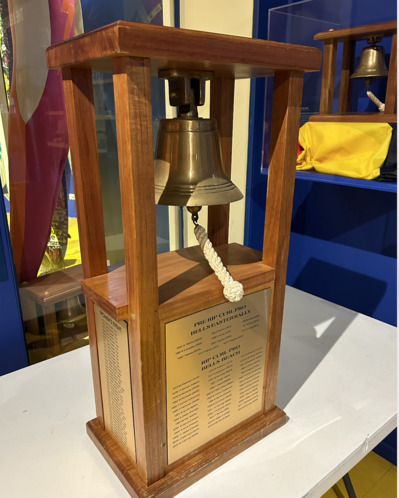
“There are only two guys who can get it out of the Otways, but even they are being stopped now with their sustainable methods. It’s scarce, but it’s beautiful.
“Every year it varies. Some years you get beautiful fiddleback guitar quality blackwood and some years you get knotty bits. It’s a beautiful timber.”
He said making the trophies was usually a six-week process.
“I don’t do it all in one shot.
“There are multiple stages. It’s sourcing the timber, its machining it, it’s ordering the bells, sanding, it’s a couple hours here and there. It’s also all about having the right quality tools.
“I have a ships chandler who casts the bronze bells in Melbourne. They are amazing quality bells, and we have different size ones for first and second place.”
Generally, the rule with the bell is you’ve got to win it to ring it, however Sweeney notes he has had to ring it from time to time to make sure everything is working in order.
Sweeney laughingly said watching the surfers ring the bell is the most nerve-racking moment of the year in his family household.

“When they shake the hell out of it on stage, we are all gripping each other’s hands saying don’t break, don’t break!
“They really shake it. They’ve just won Bells after all. They want to put it through its paces.
“It’s a nervous, yet proud moment.”
Sweeney said he plans on continuing the bell-making tradition for many years to come.
“I’m not sure where it’ll go from me, the girls [my daughters] don’t do woodwork.
“As it goes in the Jarosite band song Hey Joe Sweeney – not all men get to make a bell. So, it’s pretty cool.”