Geelong spearheads new circular wool production method
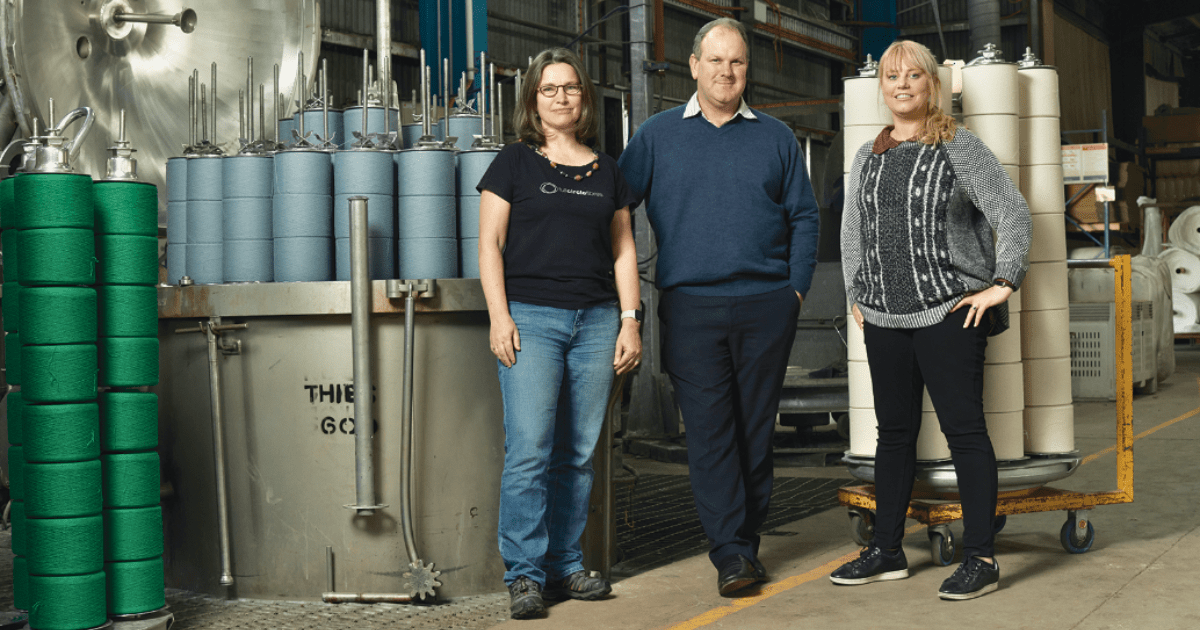
Full Circle Fibres founder Meriel Chamberlin, Deakin University Associate Professor Dr Chris Hurren and Geelong Textiles Australia commercial manager Samantha Yearwood. Photos: SUPPLIED
GEELONG industry and researchers will partner for an innovative manufacturing process aimed at creating more sustainable clothing fibres from Australian-grown wool.
Deakin University and local fibre prducers Geelong Textiles and Geelong Dyers are part of the innovative Mud to Marle pilot project, which will aim to transform the country’s clothing production supply chains and keep the region at the forefront of the national wool industry.
Mud to Marle aims to turn waste fibres into wool and cotton blend products that are spun, knitted, woven and dyed in Australia in an end-to-end on-shore process.
It will focus on circularity by using natural materials instead of plastic-based products and aims to demonstrate the sustainable technology is scalable in Australia to bring more manufacturing to local shores.
Deakin Institute for Frontier Materials Associate Professor, Dr Chris Hurren said between 60 and 70 per cent the world’s textiles are made from polyester – a synthetic fabric that has negative environmental impacts similar to that of plastic.
He also said the most processing of Australian wool and cotton happened offshore, and that the pilot aimed to bring more manufacturing close to home.
“The whole concept of this is to show that we can do environmentally-sustainable textile manufacturing in Australia,” he said.
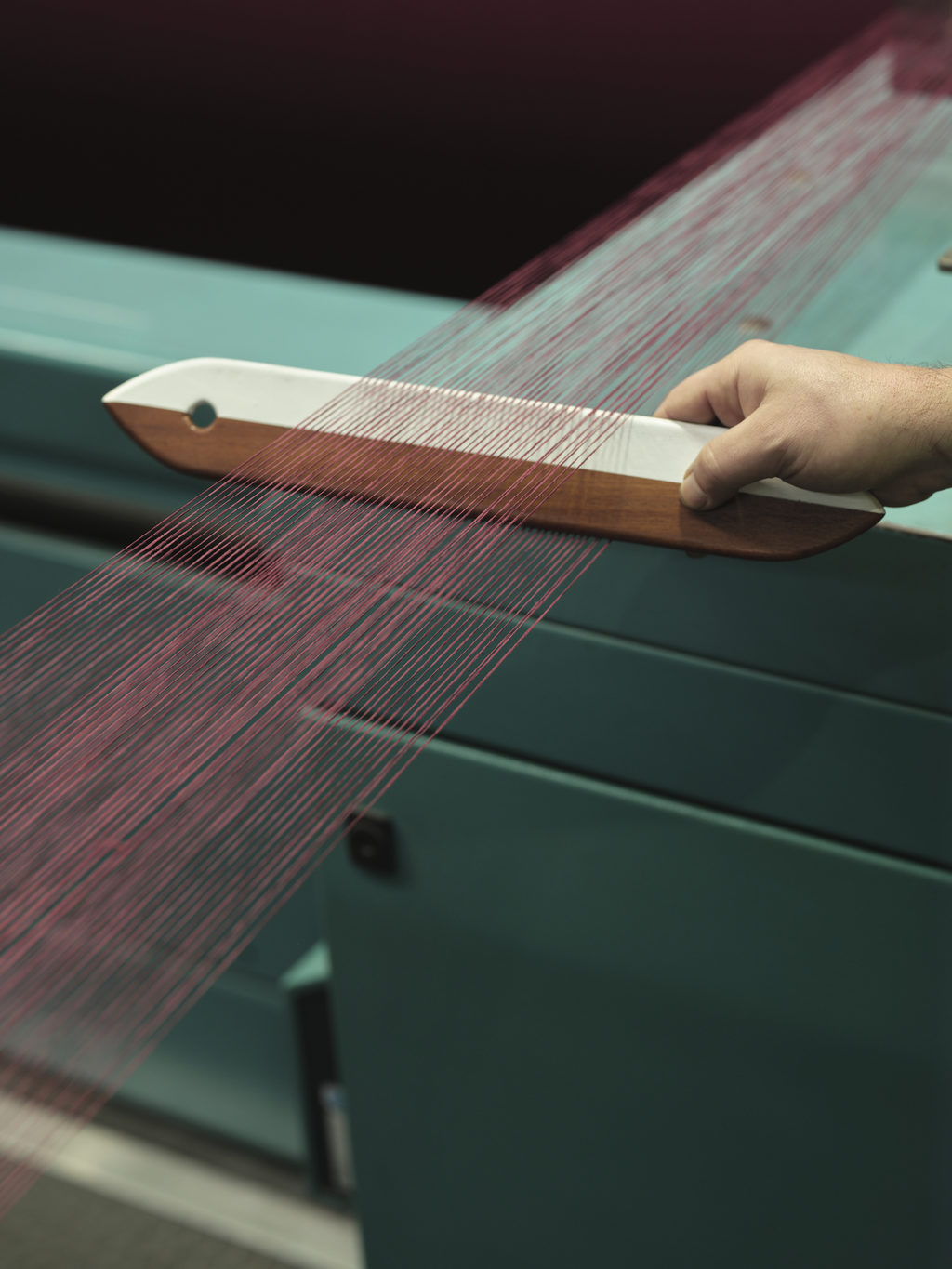
“We’re capable of making a product that at the end of its lifetime can go back into the soil again and be circular in its nature.
“We’re trying to show a whole range of different ways of adding sustainability to the product.”
He said that colouration of textiles is also the most energy-intensive part of clothing production, with a new proposed wool-dying method proposed to drastically reduce the carbon footprint of the process.
“The typical person buys 27kg of textiles a year, and if we can reduce the impact of several of those kilograms or more, that is a benefit to the environment,” Dr Hurren said.
Production will happen at Breakwater factories of the local manufacturers using common industrial equipment.
Geelong Textiles Australia commercial manager Samantha Yearwood said the business was “really excited” to be part of the trials.
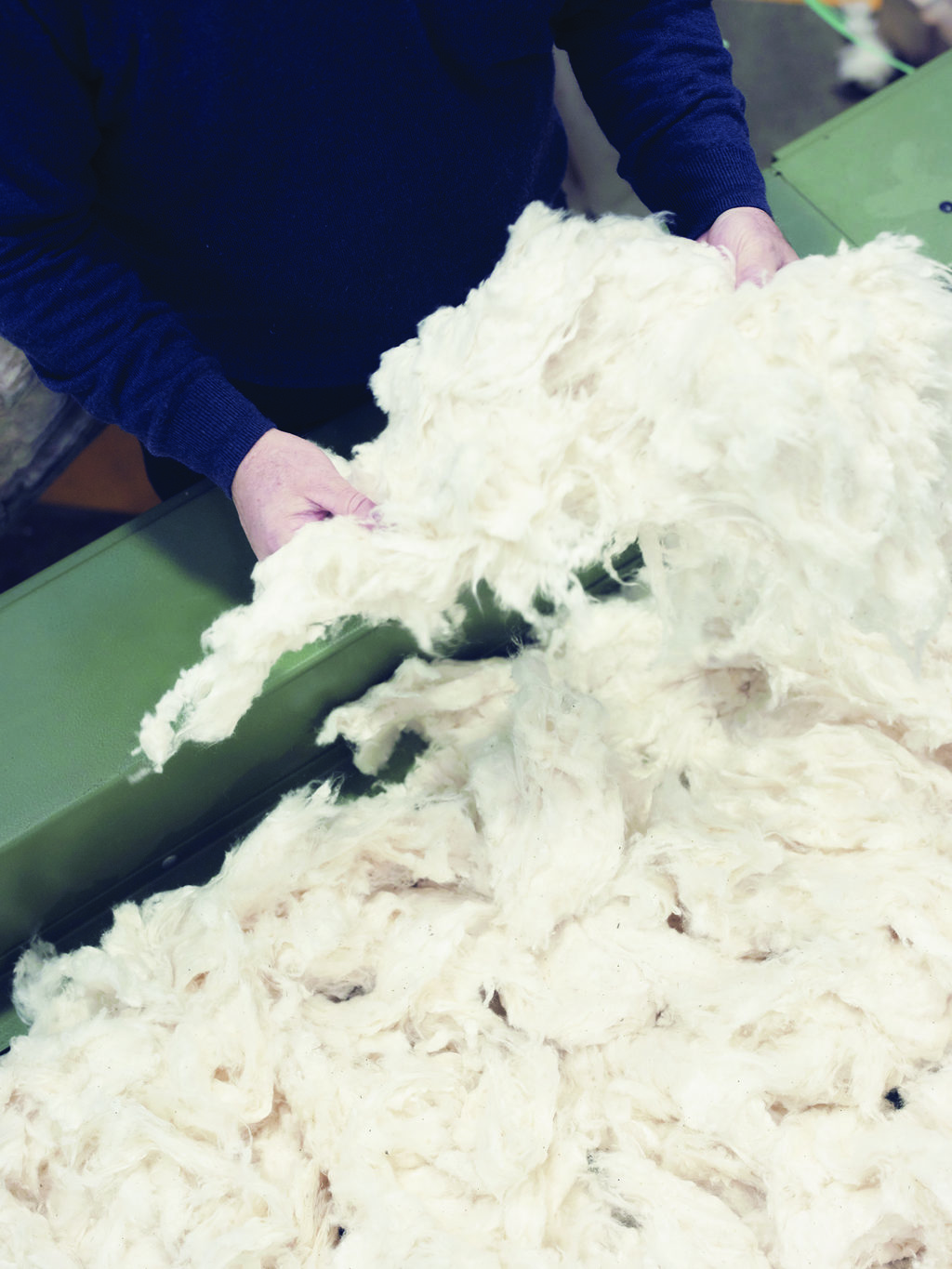
“This project takes an opportunity that’s unusual, taking a lower grade, shorter wool, and designing a product made with the lowest impact milling footprint we can engineer, yet to create a premium product optimising the natural properties of both fibres.
“Our unique combination of milling capabilities and extensive industry experience is here to be applied in new ways, and this is a marvellous example of harnessing this for the low impact and genuinely sustainable products of the future.”
Mud to Marle is a fashion industry collaboration led by B Corp-certified social enterprise Full Circle Fibres, alongside producers Ridgehaven and Australian Supper Cotton.
It was named this week in a finalist of fashion brand Country Road’s inaugural Climate Fund.
The brand will provide $147,000 of funding to the pilot and its research value, and act as an industry mentor to the local organisations.